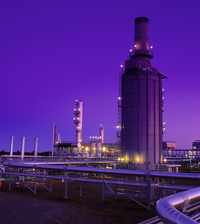
Adsorption dehydration units can reduce the water content of a gas stream to less than 0.1 ppmv. The gas industry normally uses adsorption dehydration units upstream of a liquefied natural gas (LNG) plant or a deep natural gas liquid (NGL) extraction plant where the gas temperature reduces to less than -160 °C (-256 °F) and -100 °C (-148 °F), respectively. Removal of water content to this very low level is essential to prevent freezing. This month’s article discusses feed gas flow rate, pressure, and temperature effect(s). [Keep reading]