This Tip of the Month will discuss energy issues in the U.S, and highlight why there must be an “all of the above” approach to electricity generation technologies to ensure availability and reliability. The type of technology selected should be based upon what the local resources and environment can provide as there is no silver bullet, or one size fits all solution. Energy density of the various electricity generation technologies will be covered, and some examples of current performance will be examined. [Keep reading]
Our Blog
Hydrogen sulfide and carbon dioxide are the principal objectionable acid gas components often present in natural gas, synthetic gas, and various refinery gas streams. These acid gas components must be removed for corrosion prevention in gas pipelines, process equipment, and for health and safety reasons. Reference [1] provides current acceptable concentration levels for these acid gases in various gas streams. Hydrogen sulfide removal often requires the production of sulfur in the sulfur recovery units to meet emission limits. Sulfur is a product used to produce sulfuric acid and fertilizers. Carbon dioxide removal is used for enhanced oil recovery and is required for carbon capture and sequestering (CCS) operations. [Keep reading]
Existen tres unidades claves de procesamiento, vis. Unidad de Remoción del Gas Acido (AGRU/URGA), Unidad de Deshidratación por Tamices Moleculares (MSDU/UTMD), y la Unidad de Remoción de Mercurio (MRU/URM) que son comunes tanto en el procesamiento del gas, así como facilidades del GNL. En este Previo del Mes (PDM), se analizaran algunos problemas operacionales asociados con estas unidades de proceso, y las acciones de solución en sitio (troubleshooting) de estas circunstancias operacionales. La clave para lograr una operación exitosa de estas unidades es el entendimiento de los parámetros que ocasionan la problemática operacional y como detectar estos en la fase de diseño del proyecto. [Keep reading]
There are three key processing units, viz. Acid Gas Removal Unit (AGRU), Mol Sieve Dehydration Unit (MSDU) and Mercury Removal Unit (MRU) that are common in both gas processing, and LNG facilities. In this TOTM, we discuss some common operating problems associated with these process units and suggests ways to troubleshoot the root cause of these operational issues. The key to successful operations of these units is the understanding of the parameters that cause the primary operational issues and address these at the design stage of the project. [Keep reading]
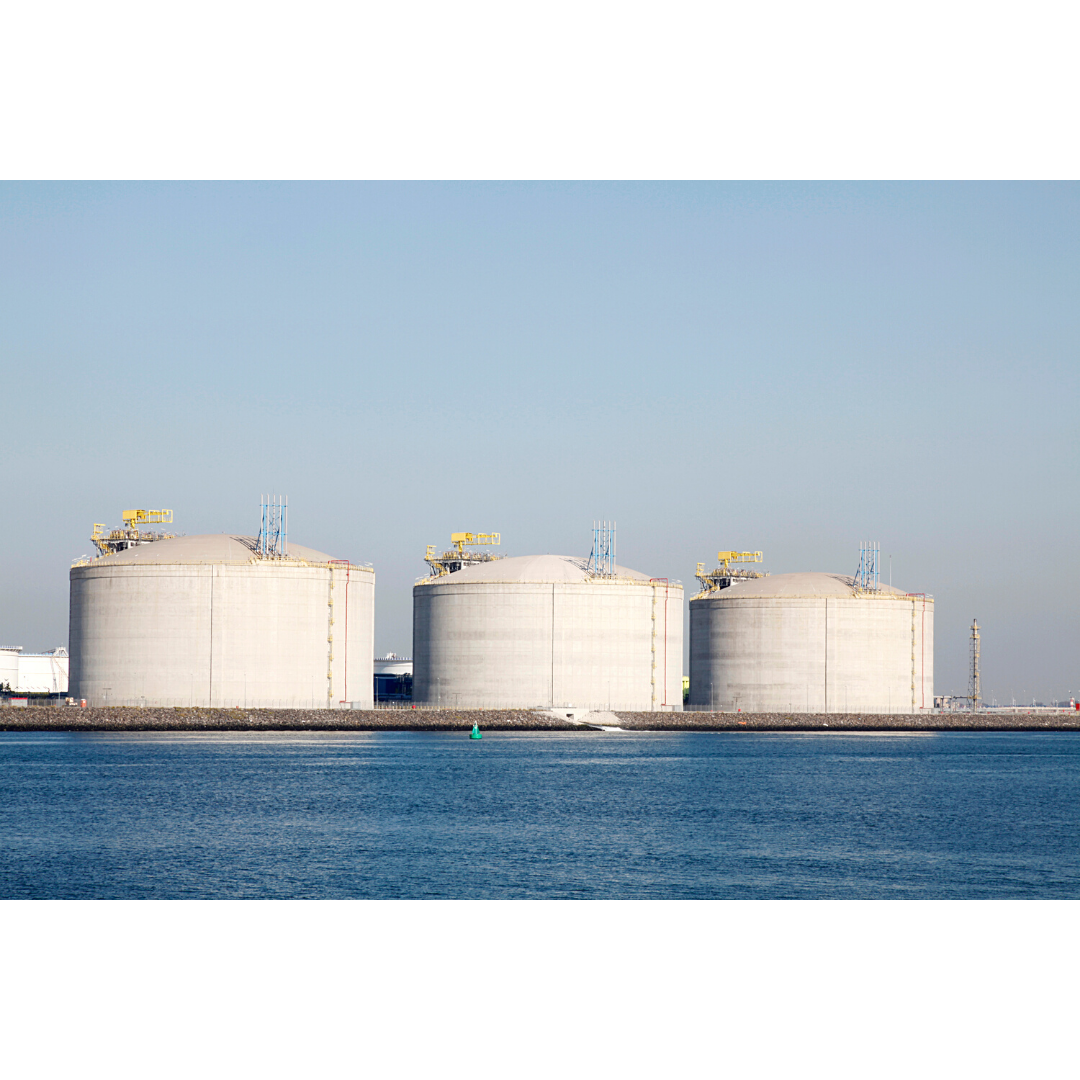
The construction costs of LNG storage tanks are very high, mainly due to the availability and cost of nickel. Most LNG storage tanks built in the modern era use 9% wt nickel steel as the materials of construction because of the materials well documented toughness at cryogenic temperatures. This article looks at advances in cryogenic metallurgy in order to reduce construction costs while maintaining a safe operational environment. [Keep reading]
During the COVID 19 pandemic, all face-to-face training came to a hard stop in March of 2020. As a training organization in the Oil and Gas Industry with a large offering of face-to-face training courses, we were faced with a significant challenge to quickly convert our course offerings to virtual delivery. Our success in the conversion of the materials to be appropriate for virtual delivery, as well as the training of our instructors to deliver this content virtually was key to our financial stability this past year. As an organization serving the industry, we feel that it is important for us to share our lessons learned on this journey to help others currently working on the path of virtual training delivery options for their own companies. This Tip of the Month will discuss tips for tools, methods, materials, and structure that can be used to create successful virtual training options. [Keep reading]